Automation is becoming a necessity across many industries, and packaging is no exception. Businesses are increasingly moving towards automated packaging solutions to improve production efficiency and reduce waste.
Before adopting packaging automation, it’s imperative to prepare your business for the process. This guide will provide the knowledge you need to make the transition to automation seamless.
What Is Packaging Automation?
Packaging automation refers to using machines and technology to handle various packaging processes—like filling, sealing, labeling, or palletizing—without human intervention. Businesses can replace laborious tasks with machines to supply consistent outputs.
Automation technology leverages programmable logic controllers (PLCs), robotics, and sensors to improve operations. These components work together to enhance speed, accuracy, and efficiency while reducing the risk of error.
Systems like horizontal pouch packaging machines can automate filling and sealing premade pouches with precision. They are particularly useful for businesses that handle high-volume packaging operations, such as food, beverages, and personal care products.
By streamlining the packaging process, automated machines reduce manual labor and increase productivity. Their reliability makes them essential for companies looking to optimize their packaging workflow.
How Does Packaging Automation Work?
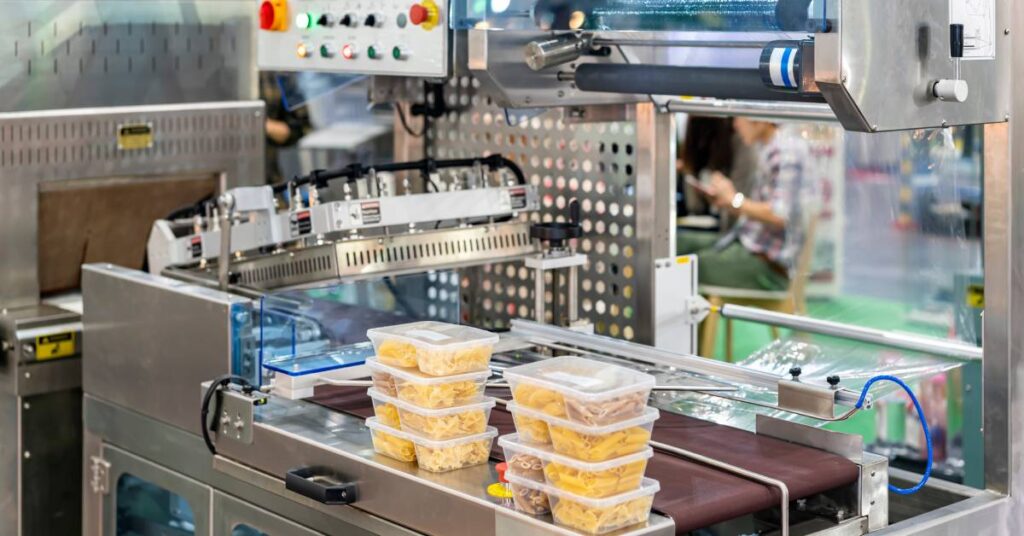
Though designed to suit specific objectives, all automated packaging systems follow a common workflow. Here’s what that process looks like:
- Material handling: Machines move packaging materials like pouches, cartons, or film rolls into position.
- Filling and sealing: The product is dispensed into the packaging using precision filling systems, providing consistent weight and volume. The machine seals the package using heat, adhesives, or ultrasonic methods.
- Labeling and coding: Labels, barcodes, expiration dates, and other details are promptly applied to the packages.
- Inspection: Sensors and cameras inspect the products for quality control, detecting defects or inaccuracies in real time.
- Secondary packaging: After primary packaging is complete, the products are ready for the shipping stage by grouping them into boxes or pallets.
Why Invest in Packaging Automation?
With automation, businesses can achieve greater efficiency, reduce time spent on tasks, and decrease costs and waste. This leads to improved operations and higher profitability.
Consistent product quality, customer satisfaction, and safer workspaces are all achievable. By removing people from risky or repetitive jobs, automation minimizes injuries and maximizes outputs.
Having a thoughtful implementation strategy in place will improve your business’ success potential. This includes evaluating current processes, selecting the right tools and technologies, training staff for the adjustment, and integrating the new technology smoothly into existing workflows.
Implementing Packaging Automation
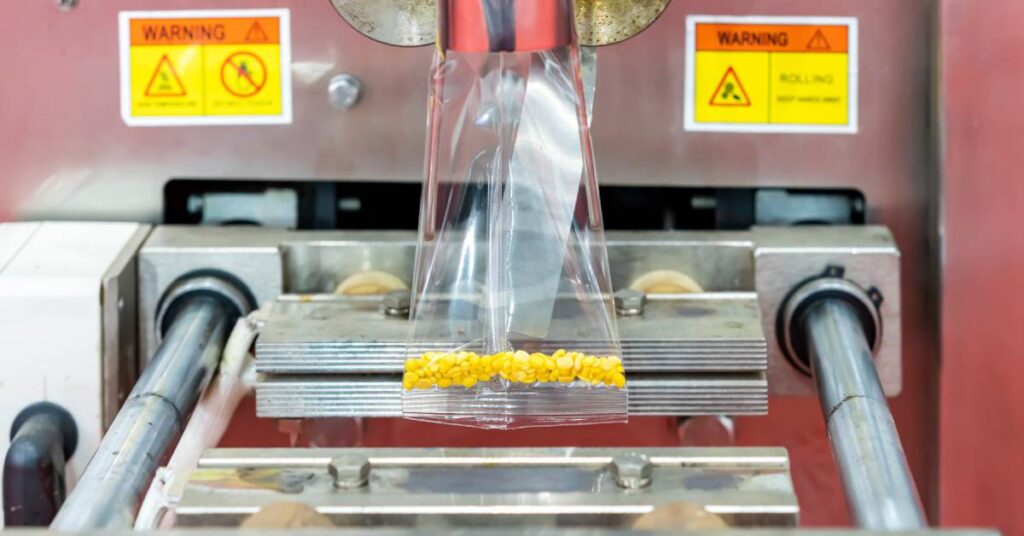
Transitioning to these systems isn’t as simple as purchasing the latest equipment; it’s a complex process that requires preparation. Below, we’ve outlined key steps to guarantee the success of your efforts.
1. Evaluate the Business’s Packaging Needs
Begin by analyzing your current packaging methods to identify points where automation can improve operations. Assess which processes are labor-intensive, where production decreases due to inefficiencies, and the outcomes you aim to achieve, like boosting speed or refining quality.
For instance, businesses that regularly seal large volumes of pouches could benefit from a horizontal pouch packaging machine designed to handle high-speed operations. Addressing this wide range of questions from the start will align your goals with the best automation solution.
2. Set a Realistic Budget
While automation can trim costs in the long run, the initial investment is considerable. Businesses face various expenses when adopting new technology, involving buying and installing the equipment. Check that it will work seamlessly with existing systems. On top of that, operators need the right training to use the technology effectively and confidently.
Ongoing maintenance is also necessary to continue running the systems smoothly. To make the process more manageable, work with a supplier who can design a solution tailored to your financial constraints and business demands.
3. Choose the Right Equipment
Select machines that align with your operational needs and scale. Options range from compact systems for small businesses to fully integrated production lines suitable for large manufacturers.
At HMC Products, we offer a wide range of packaging solutions, including horizontal pouch packaging machines. With a focus on customization, we help businesses seamlessly transition into automation.
4. Design the Facility Layout
Your current workspace must be suitable for the new equipment. Consider factors such as the availability of floor space and access to utilities like power and compressed air.
It’s important to involve all affected departments so that the transition is simple. This includes operations and maintenance teams. Their input will help address many aspects of the new layout to optimize the workflow and minimize disruptions during operation.
5. Train Your Workforce
Automation doesn’t eliminate human involvement; it shifts the focus to managing, monitoring, and maintaining the system. Invest in training programs to sharpen your workforce’s skills. Operators should understand:
- how to efficiently use and troubleshoot the machinery,
- the best maintenance practices to extend the equipment’s lifespan,
- and the importance of quality control in automated systems.
A proactive approach will reduce downtime and build employee confidence in the new system.
6. Test the System Before Full-Scale Implementation
Before rolling out automation technology across the entire operation, start with a trial run. This phase allows you to:
- identify potential issues in a controlled environment,
- fine-tune system configurations to improve efficiency,
- and collect feedback from machine operators and supervisors.
Pilot testing helps you identify and tackle challenges before they escalate into major obstacles.
The Long-Term Effects of Automation
While the initial transition takes time, effort, and resources, thorough preparation will help you maximize the long-term benefits. Developing a clear implementation strategy, training your team, and allocating the right resources upfront can make the transition more effective.
Beyond the initial setup, maintenance and continuous improvement should always be part of the plan. Conducting regular inspections, updating software, evaluating performance, and implementing feedback loops efficiently maintain your systems. They also remain scalable and adaptable. Proactive thinking will minimize disruptions and continue to deliver consistent value.
Start Integrating Automated Technology Today
Integrating automation into your operations marks a progressive shift that enhances efficiency and long-term growth. By following these steps, you’ll not only achieve short-term productivity gains but also position your business to remain competitive with fellow businesses.
Whether you’re exploring a horizontal pouch packaging machine or other automated solutions, taking the time to prepare your business will ease the transition and set the foundation for success.
For guidance tailored to your specific needs, connect with HMC Products. We’re ready to offer expert advice and innovative solutions for your business.