Packaging equipment can streamline operations, boost efficiency, and increase productivity. However, many business owners and packaging managers may not be aware of the extra expenses that can derail budgets. Whether you’re scaling up the production line or upgrading outdated hardware, learn about the hidden costs of buying pouch packaging machines.
1. Installation and Commissioning Fees
After purchasing a machine, you’ll need to allocate resources for installation and commissioning to confirm it works correctly. These services involve skilled technicians who assemble components, calibrate the equipment, test the machines, and guarantee they perform correctly.
In some cases, this process may also include training your team to operate the machines. Depending on the complexity and size of the equipment, the cost for setup and testing can vary widely because of travel factors or the use of specialized tools. These expenses may be excluded from the initial price, so budget separately to avoid surprises.
2. Customization Costs
Every production environment is different, and off-the-shelf configurations frequently don’t meet all operational needs. Customizing a machine to fit specific pouch sizes, sealing patterns, or production speeds can quickly increase costs. Be sure to evaluate your operation requirements thoroughly before committing to a purchase.
Work closely with equipment manufacturers to determine customization options and potential lead times. Test prototypes or sample pouches for compatibility before full-scale production. Regularly review machine performance to identify areas for further optimization.
3. Spare and Replacement Parts
After continued use, certain components will need replacing. Essential parts like sealing jaws, belts, and motors may need to be kept in stock regularly. Even if the initial machine came with spares, the ongoing expense of keeping a stockpile can add up. Some pouch packaging machine manufacturers charge a premium for these parts, so it’s worth asking about availability and pricing upfront.
Verify if the manufacturer provides warranties that include spare parts. Confirm that any replacements are compatible with your model to perform effectively. Regular inspections can help spot early signs of wear and minimize downtime.
4. Training Costs for Operators
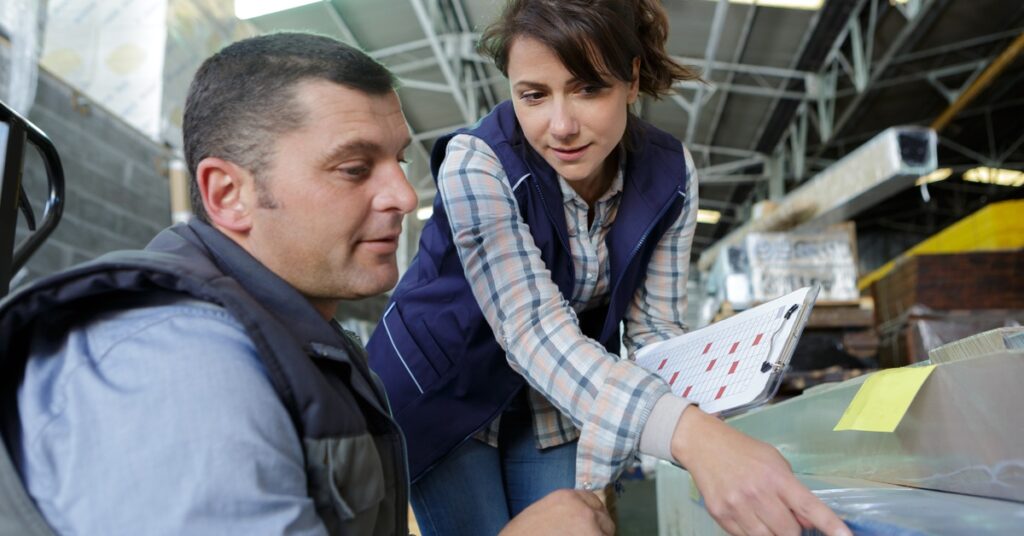
A new machine will require staff training, which inevitably demands additional time and money. Untrained operators can make mistakes, leading to downtime or damaged equipment.
Adequate training enables operators to use the machine safely and efficiently. Some businesses prefer on-site training while others will sign up for remote instruction.
Look for manufacturers that provide detailed training manuals or video tutorials for comprehensive training and future support. Troubleshooting guides and customer service hotlines can help address issues quickly.
5. Energy Consumption
High-tech machinery can hike up the facility’s electricity consumption if it doesn’t include energy-efficient features. In this case, you’ll need to expect the monthly energy bills to increase, particularly if your facility has multiple shifts or runs 24/7.
Be sure to examine the machine’s specifications and understand its energy requirements before purchasing. Furthermore, consider investing in machines with energy-saving modes to reduce operational costs.
Regular maintenance can also improve energy efficiency and prevent unnecessary power usage. By monitoring your facility’s energy consumption, you can figure out peak usage times and adjust accordingly.
6. Maintenance and Service Contracts
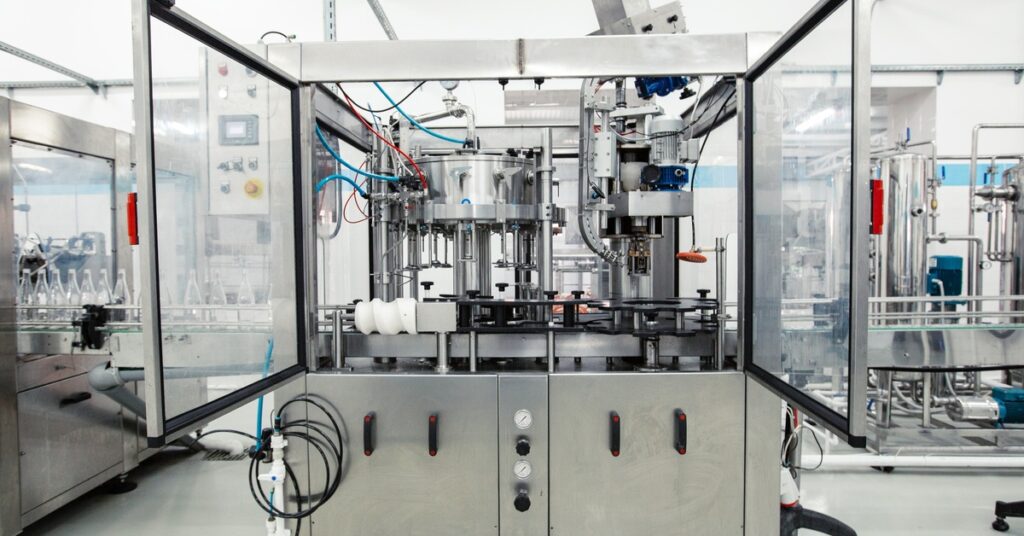
Preventative maintenance is a must for keeping packaging machines in working order, but service contracts with manufacturers are expensive. While some manufacturers offer initial warranties, extended service agreements come at a premium. Compare what’s included in the service contract versus what additional costs might crop up for unscheduled maintenance.
7. Downtime Losses
Unplanned downtime can disrupt production schedules and create bottlenecks in your operation. Machines that aren’t properly serviced or designed to meet the facility’s capacity can lead to costly delays. Factor in the opportunity cost of idle machines and how they could affect customer deadlines or lead to inefficiency.
Worn equipment can drive up maintenance costs, but thorough training and high-quality tools can diminish expenses. Providing refresher courses for machine operators will prevent misuse that leads to breakdowns. Pair this with predictive maintenance tools to detect issues early and avoid disruptions.
8. Software Licenses and Updates
Most modern pouch packaging machines include smart software for enhanced efficiency and diagnostics. While this technology is beneficial, software licenses and updates are frequently overlooked costs.
Some manufacturers may charge annually for system upgrades or monitoring tools. Confirm what software features are included in the purchase price. Ask if optional upgrades come with additional fees.
9. Freight and Delivery Costs
Freight costs aren’t typically included in the initial quote, especially for large or international orders. Packaging machinery tends to be heavy, so it requires specialized trucks or shipping methods. When machines need transporting in multiple sections, you may also face additional reassembly costs.
10. Integration With Existing Systems
If your pouch packaging machine requires integration with upstream or downstream processes—like filling, capping, or labeling machines—specific software or accessories may be necessary. Unforeseen costs may arise from creating custom connectors or programming, depending on how compatible the new machine is with your existing setup.
11. Compliance Costs and Regulatory Adherence
Some industries need to abide by strict regulatory compliance requirements for safety, hygiene, or environmental standards. For instance, food and beverage companies must meet guidelines from the United States Department of Agriculture (USDA) or the Food and Drug Administration (FDA) for packaging machines. Meeting all required certifications for the machine may increase expenses for inspection, validation, or modifications.
How To Plan for These Costs
Acknowledging the hidden costs of buying pouch packaging machines is the first step toward securing the investment. Many manufacturers don’t provide a complete breakdown of associated costs upfront, so it’s important to ask the right questions.
At HMC Products, we’ve helped businesses of all sizes improve their packaging lines with reliable equipment. Our team focuses on ensuring you’re aware of—and prepared for—all potential costs. This is the best way to avoid wondering what expenses come next after the initial purchase.
The Bottom Line
Picking the right pouch packaging equipment is only one aspect to focus on. From installation fees and training to energy costs and compliance, unexpected expenses can add up quickly. Businesses that understand the full aspects of ownership can prepare for these contingencies and prevent disruptions to their production lines.
If you’re considering investing in a packaging solution, take your time to evaluate all potential costs. Having a detailed plan will help you stay within budget and achieve long-term operational success.
For more information on reliable equipment and expert support, contact HMC Products.