The busiest seasons are a challenge for any business dealing with high demand and tight deadlines. These periods, often coinciding with holidays or industry-specific trends, require businesses to increase production efficiency. The key to meeting demand is preparing for peak seasons with the right packaging machine. Reliable equipment refines your operations and prevents bottlenecks.
From small-scale manufacturers to large production facilities, adequate packaging solutions achieve success.
1. Understand Your Peak Season Challenges
Analyze the unique challenges of the busy months before selecting a packaging machine. Consider factors such as higher volume demand, diverse product lines, increased shipping requirements, or space constraints in your facility. Knowing how you’ll need to adjust will make it easier to select the most effective equipment.
For example, if you expect to package fluid or granular products like sauces, powdered foods, or detergents, a horizontal pouch packaging machine may be a smart choice. It’s versatile and precise for sealing, regardless of product type.
2. Evaluate Your Current Equipment
Does your current packaging equipment keep up with high demand, or does it create bottlenecks?
Take an honest assessment of its performance. Is it struggling with accuracy, speed, or consistency? Frequent maintenance issues during peak operations are telltale signs that your machine may need an upgrade or replacement.
Investing in advanced machinery can prevent breakdowns mid-season that disrupt workflows and cost valuable time—sometimes when it’s least expected. HMC Products offers reliable equipment to meet industry standards during busy periods.
3. Select Machines That Match Production Speeds
During peak seasons, keeping up with fast production cycles without compromising quality is a priority. Choosing a machine with sufficient throughput to meet your busiest moments is an important decision. Figure out your average output per hour, and select packaging machines designed to complement that pace—or better yet slightly exceed it.
For high-volume projects, a robotic equipment add-on supports precise product processing. Its high-speed functionality makes it an asset for businesses juggling higher operational loads.
4. Flexibility Matters for Varied Products
Seasonal peaks often increase the diversity of SKUs. Whether you’re managing different product sizes or packaging materials, such as film, foil, or eco-friendly substrates, your equipment should allow seamless changeovers. Machines must adapt quickly to minimize downtime between product runs while supporting accuracy.
For example, the IMTE Pouchmaster is favored for its ability to handle different packaging formats, from stand-up pouches to resealable bags. Many companies use it for packaging snacks, pet food, and powdered products.
5. Train Operators Before the Rush
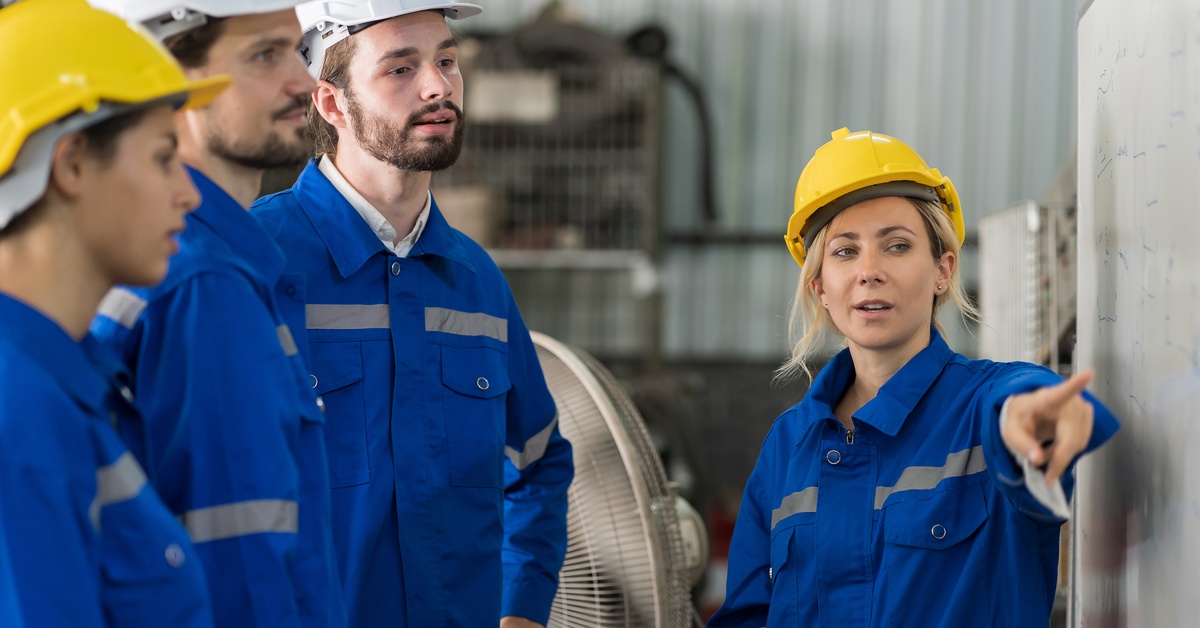
Even the best machine won’t deliver high-quality results if operators are unfamiliar with its features. Adequate training is essential.
Skilled operators boost efficiency and reduce errors, especially during increased demands. Schedule refresher courses or advanced training sessions so everyone understands how to use the machine correctly in anticipation of busier periods.
Providing staff with advanced knowledge about settings, adjustments, and troubleshooting reduces the risk of mistakes under pressure, making operations smoother and more productive.
6. Refine Workspace Layouts
An efficient packaging workflow isn’t just about the machine but also how it fits into your workspace. Review your facility’s layout to minimize unnecessary movements and improve each step of the process. Properly positioning conveyors, setting up ergonomic workspaces, and efficiently organizing space around the packaging machine significantly enhance productivity.
For compact environments or those handling multiple product lines in smaller batches, space-saving machines like the IMF Pouchmaster streamline operations without sacrificing functionality.
7. Account for Maintenance Needs
Routine maintenance is still a priority, even during high-capacity periods. Choose equipment designed for easy servicing with accessible components, enabling quick fixes or routine upkeep that doesn’t take away from production time. Regularly inspect belts, seals, and other moving parts to keep your machine in peak condition.
Streamlined maintenance cycles also enhance long-term productivity by increasing the machine’s lifespan—a worthwhile investment for achieving consistent performance throughout multiple seasons.
8. Maximize Cost Efficiency
Peak seasons often come with heightened operational costs, from raw materials to more personnel. Your chosen packaging machine should complement your budget while lowering waste and energy consumption. Machines that reduce downtime, automate repetitive tasks, and improve material use ultimately pay for themselves in the long run.
A horizontal packaging machine effectively uses materials by achieving precise cuts and seals, reducing film waste in every task. Operators can easily adjust settings to meet specific packaging requirements.
9. Leverage Testing Data for Improvements
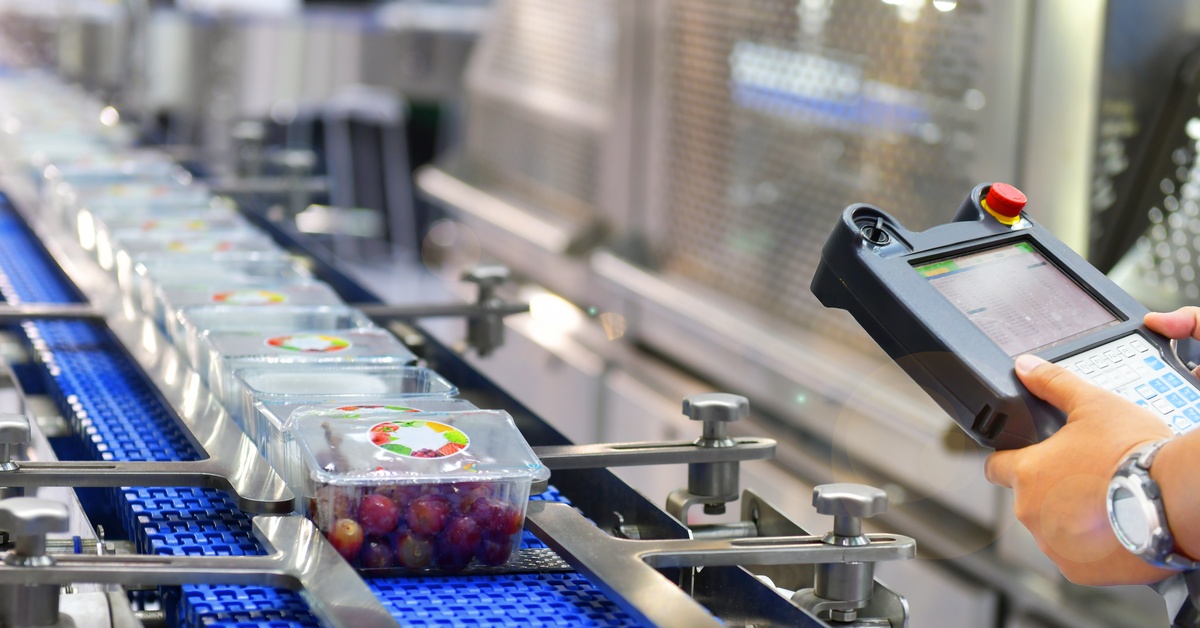
Modern packaging machines often come equipped with features that provide valuable real-time data. Metrics such as production output, error rates, and material usage can prove invaluable when analyzing season-end performance.
Use this information to find inefficiencies or areas to improve for the next busy period. Analyze material waste to improve resources and lower operational costs.
10. Purchase Ahead of Time
Don’t wait until peak season is around the corner to upgrade your machinery. Doing so could leave you cutting it too close, especially if your desired equipment has a lead time for delivery and installation.
Aim to buy and test your packaging machinery several months before you’ll need it to leave room to troubleshoot issues.
11. Test Runs Are Nonnegotiable
Conduct thorough testing with your new machinery under realistic operating conditions. Simulate expected product volumes and variabilities to ensure the machine performs exactly as needed. These test runs also allow you to identify and resolve potential setbacks ahead of time.
12. Plan for Seasonal Scalability
Today’s peak seasons could differ drastically from those in the future. When investing in packaging machinery, consider its scalability for growing operations.
Choose equipment that supports modular upgrades or add-ons so you can scale your processes as demand grows. Verify compatibility with future packaging materials or designs, and prioritize energy-efficient models to reduce long-term operational costs.
Smooth Sailing Through Peak Season Preparation
Investing in the right packaging machine prepares any business for peak seasons. Take proactive measures so your production process can stay efficient and adaptable under pressure. Training your team, upgrading your workspace layout, or introducing machines from HMC Products can set you up for success.
Evaluate your needs to avoid unnecessary hurdles when demand surges. With the right machinery and necessary considerations, you can keep operations running smoothly. Contact HMC Products today to find the perfect solutions for your operations.