Efficiency and precision are the cornerstones of a packaging operation. Understanding the back-end processes in these facilities is critical for optimizing supply chains and delivering high-quality goods. This blog covers what happens behind the scenes in a pouch packaging facility, highlighting the processes, machinery, and teamwork that drive these operations.
1. Receiving Materials
Pouch packaging begins with receiving raw materials, such as film rolls, zippers, and laminates. These materials are inspected and categorized based on thickness and barrier properties. Understanding material specifications is essential for meeting customer demands, from food-grade films to high-barrier laminates for moisture-sensitive products.
Operators will load the film rolls onto the packaging machines and align them in order to prevent errors during production. Technicians regularly monitor the machines to maintain consistent seal quality and precise cutting.
2. Material Storage and Handling
Materials are stored in temperature-controlled areas to maintain their integrity and minimize the risks of contamination or damage. Clear labeling and inventory management systems are useful for tracking and accessing materials during production.
Staff regularly inspect storage conditions to comply with safety standards. They also closely monitor expiration dates to avoid using outdated material. Finally, they will promptly remove damaged or compromised items in order to maintain quality.
3. Quality Control Before Production
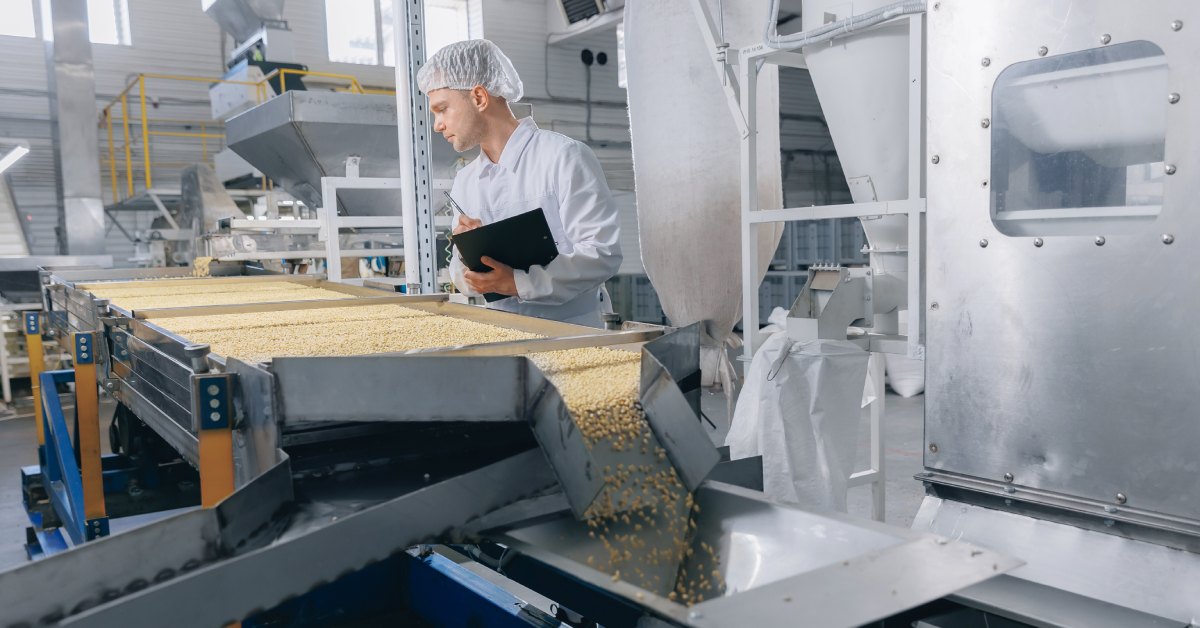
Quality control starts well before production begins. Workers will examine reels of packaging films for pinholes, scratches, or inconsistencies in the coating. Even the smallest imperfection can compromise the integrity of pouch packaging. While inspecting materials adds time to the process, it guarantees the finished product meets performance standards during transportation and on retail shelves.
Quality control teams also test the tensile strength of the films under stress. They use specialized equipment to measure heat-sealing performance and confirm that pouches stay secure. Every batch undergoes random sampling for defect and recall prevention.
4. Design Phase
Businesses with branding needs can create designs at their facility. They will finalize pouch graphics and layouts based on print-ready specifications. Digital and flexographic printing methods deliver sharp, precise images in vibrant colors.
Packaging teams and brand managers can collaborate to align their marketing intentions. They may also conduct quality checks for brand standards and technical requirements. Custom finishes, such as matte or gloss coatings, enhance the look and feel of the pouches.
5. Loading Films Into Machines
Once inspected and approved, film rolls can enter bag-making machines. These machines work to form, fill, and seal (FFS) the pouches during production. Roll placement and alignment are crucial because misalignment can cause tears, ineffective seals, or improper dimensions. Many facilities rely on top-tier FFS machine manufacturers to acquire reliable machinery.
Operators monitor the machines for consistent performance throughout production. Regular maintenance is essential to prevent mechanical issues that could disrupt the process. Advanced FFS machines also feature sensors and automation to detect errors and maintain precision.
6. Forming the Pouches
A pouch begins as a flat film. During the pouch-forming step, machines shape the material into a three-sided seal, stand-up, or flat-bottom pouch configuration. Heat or ultrasonic sealing fuses edges. The efficiency of this step depends on precise temperature control and consistent pressure from the machines.
Calibrated equipment produces tight seals that prevent leaks during packaging and transport. Polyethylene or polypropylene film are common materials because they meet most products’ storage and durability needs.
7. Filling Stations
Next, the pouches move to filling stations. Various products, such as powders, liquids, and granules, are dispensed here. Filling mechanisms vary depending on the packaging facility; auger fillers are useful for powders, and gravity fillers are ideal for liquids. The machine calibrates fill volume to meet specified weights, which abide by legal packaging requirements. Sensors detect inconsistencies in weight or volume. After filling, the pouches move to the sealing stage to prevent leaks or contamination.
8. Sealing the Pouches
Sealing is one of the most important steps in the packaging process. The machinery uses heat or adhesives to seal the pouches. This step prevents leaks and maximizes the longevity of the packaged product. Operators monitor the sealing process to catch weak seals that could compromise the product during transport. Sealing protects the product from external elements, such as moisture or air, which could cause contamination. Advanced sealing machines can handle various materials, including plastic, foil, and multi-layered films.
9. Inspection and Testing of Final Outputs
After sealing, completed pouches go through another round of inspection and testing. Leak tests, burst strength evaluations, and drop tests simulate real-world conditions to verify that the pouch can handle the rigors of transit and storage. Occasionally, automated vision systems detect cosmetic defects, such as misaligned branding, uneven fills, or tears. Defective pouches are removed before packaging to maintain high standards.
10. Secondary Packaging and Labeling
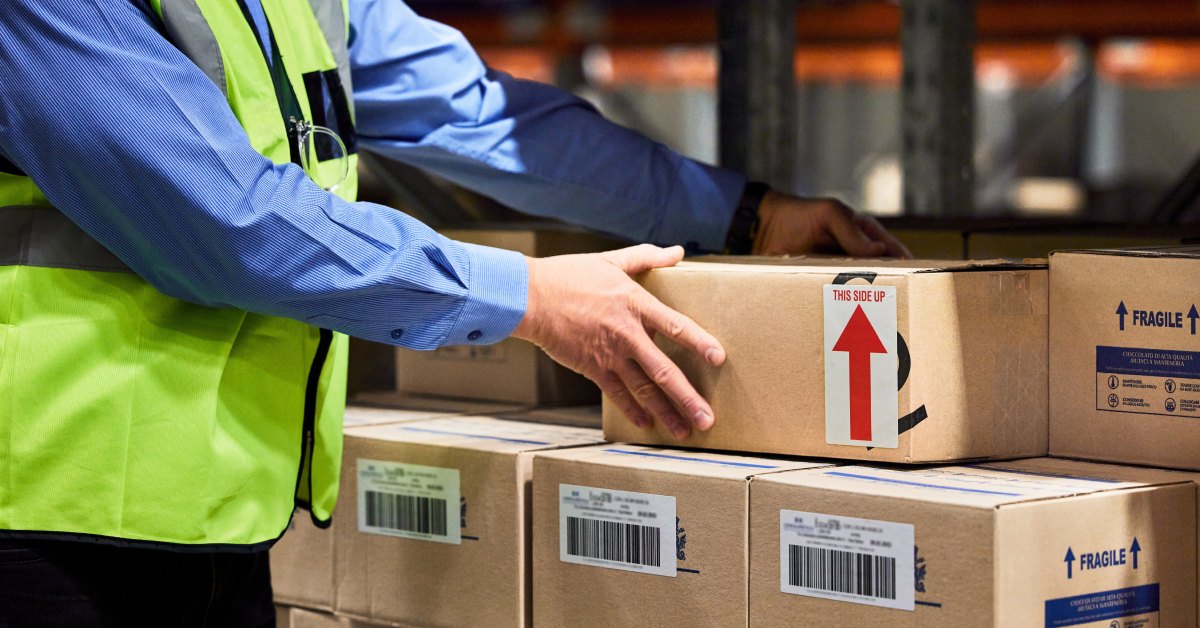
Finished pouches are arranged into cartons, trays, or shrink wraps to prepare them for transport. Labeling includes batch numbers, barcodes, and expiration dates, and this occurs before the pouches are packed. Workers use automated systems to streamline this step since accuracy and traceability are essential for inventory record-keeping. The labeled cartons are sealed once more to protect the products. Finally, packages are organized for loading onto delivery trucks.
11. Shipping and Logistics
Products are carefully loaded onto trucks, palletized for stability, and prepared for distribution channels. Facility managers will coordinate closely with supply chain management teams to minimize delivery times and uphold product quality standards. Drivers follow optimized delivery routes to remain on schedule, and each shipment is tracked to provide updates on delivery progress.
Why Transparency Matters in Pouch Packaging Facilities
Understanding the intricate processes behind the scenes in a pouch packaging facility sheds light on the complexity of these operations. From the precision of the pouch-forming stage to the engineering of the final seal, every step requires collaboration between skilled workers, advanced machinery, and quality control teams.
If you want to incorporate top-of-the-line solutions for your packaging operations, HMC Products delivers machines optimized for cost-effectiveness, speed, and accuracy.
Pouch packaging protects product integrity, shelf life, and supply chain efficiency. By partnering with HMC Products, you can achieve optimal packaging outcomes while standing out in competitive markets.